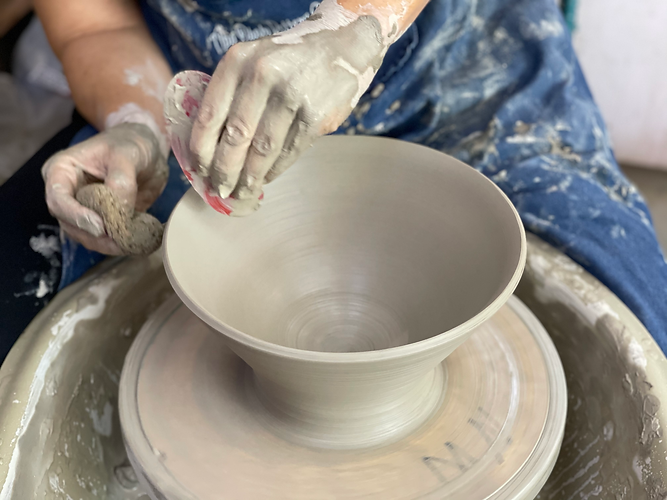
THE PROCESS
Find out more about my process below.
I usually start by designing an item and then test it on the pottery wheel. But sometimes it’s the other way around; (the clay I use shrinks about 10-12% so I need to throw my pieces slightly larger than the desired final result).
I document each step on my notebook. It allows me to go back to any random pot I made years ago and find out all the information to recreate or revisit the design.
The newly created piece will dry for about a day before becoming “leather hard”, a stage when they are firm to the touch but still contain a lot of water which gives them this perfect consistency for trimming into their final shapes.
The trimming is where I spend the most time, as I do not particularly enjoy sanding my pieces after the first bisque firing. I make sure I smooth as much as possible each object. I then sign/stamp each piece on the base and leave them to dry for about a week, (first couple of days under plastic to allow a slow even drying of the object and avoid cracks ).
When completely dry, my work can go for the first firing called the “biscuit or bisque firing”. The firing takes about 20 hours (approximately 10 hours to reach the temperature of 950 degrees Celsius) and as much time to cool down to about 100 degrees Celsius when I can safely open the kiln.
The next stage is sanding each piece to remove any sharp edges and irregularities (this is the part I like the least) then I wash the dust off, leave it to dry for another day before I can glaze (adding color). I use different kind of glazing techniques depending on what results I want, dipping, pouring, and even brush on.
Note that as potters, we do not have complete control on the result of the glaze firing. ….Some glazes are very reliable but I like to also use a good amount of those more “unreliable glazes” that flow and run and give each piece a very unique result. By mixing my glazes and changing the way I apply them, I take a few more risks but it’s nice to let go of any expectations!
After that, the pieces are ready for their final firing, “the glaze firing”. I usually fire porcelain and stoneware clays to 1250 degrees Celsius and wait impatiently for 24 hours to open my kiln.